“Racing is a great mania to which one must sacrifice everything, without reticence, without hesitation.”
This project began with…
the AeroTestra Mk 10 ducted fan multirotor UAV. Through my research I felt I could design an VTOL (vertical take-off and land) aircraft that would produce higher “lift”, more efficiently and more quietly than non ducted propellers. While significant efficiencies were realized, the manufacturing process was overly burdensome for small scale aircraft.
With this information and a ever growing interest in human payload capacity, development of the UAV acted as a foundation for much larger, electric aircraft Given the requirements for efficiency, safety, and redundancy, it is likely most electric VTOL aircraft that are designed for humans will employ a similar propulsion design.
All of the concept below are renderings based on detailed CAD models.
AeroTestra Mk 10 was designed as a highly efficient, 5 kg payload delivery and imaging system unmanned aerial platform.
AeroTestra’s Personal Electric Racecraft
Full carbon fiber monocoque fuselage
Hydrogen fuel cell power supply
Exceptionally high thrust to weight ratio
Thrust vectoring allows for precision maneuverability
Articulating Ducts
The most important design iterations to be driven by the first prototype were the need for articulating ducts. This is to counteract two problems introduced by ducting the propellers. The first issue is known and relates to a duct that is pitched forward will want to return to a horizontal orientation. The second issue arises from a lack of yaw authority due to diminished “prop tip” drag. Both of these issues are addressed by the articulation of the ducts
Detail of articulating bearing
Two Stage Turbine
Because the aircraft is already obligated to the weight of the ducts and supportive structure, it would follow reason to maximize their use. Having two “fans” progressively increasing the airspeed through the duct is more efficient use of the duct than a single propeller.
Thrust efficiency can be optimized through the use of variable pitch rotors controlled by adaptive “intelligent” motor control and monitoring systems. This also opens the possibility of utilizing auto rotation in cases of complete power failure.
Go Speed Racer! Go!
Racing into the future…
It seems to me that a “racecraft” is a logical first step towards the development of high performance electric aircraft. The motivation for humans to go faster and and higher will never leave us until we have democratized the heavens the way we have the earth. This “goal” will push the technologies that will act as the foundation to modern electric aviation.
Personal electric aircraft similar to the design I describe here use advanced technologies in composite fabrication, motor design and control, and embedded autopilot control systems. Having said that, everything involved in the realization of this aircraft is fundamentally tested and sound.
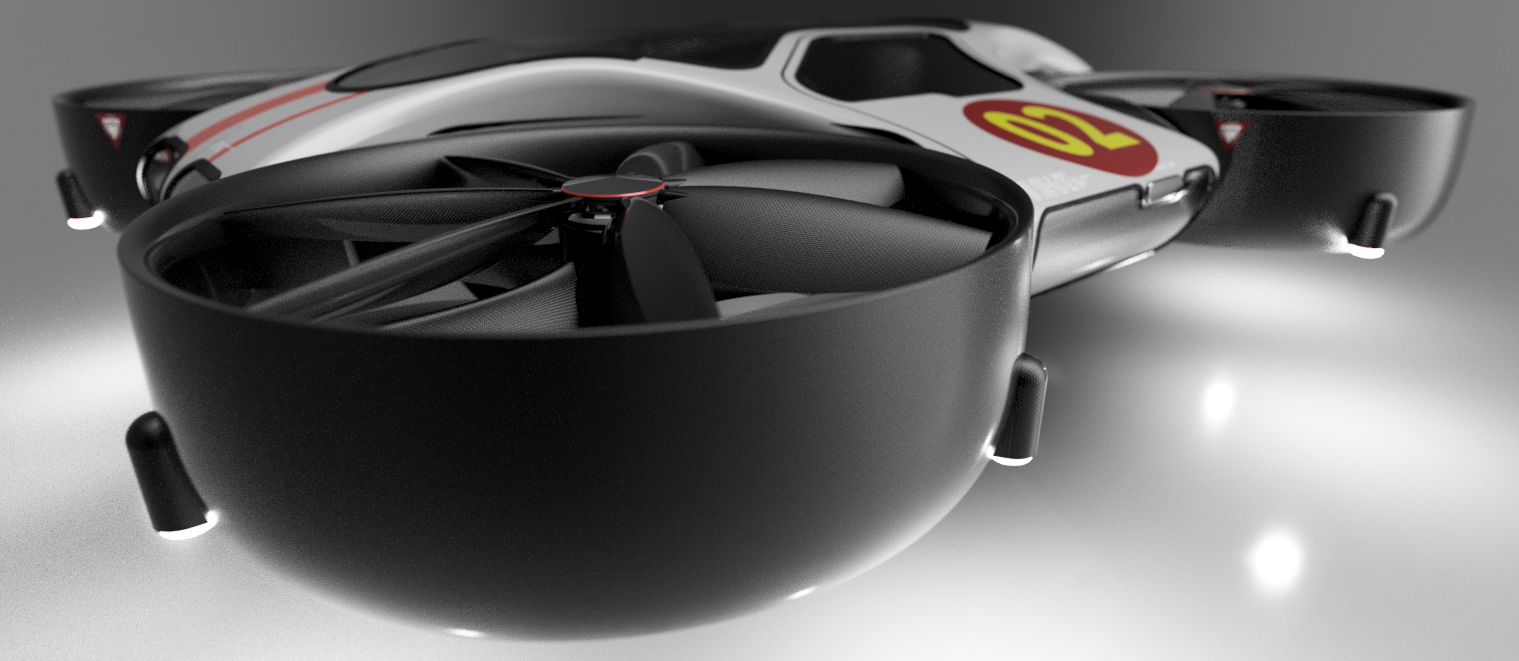
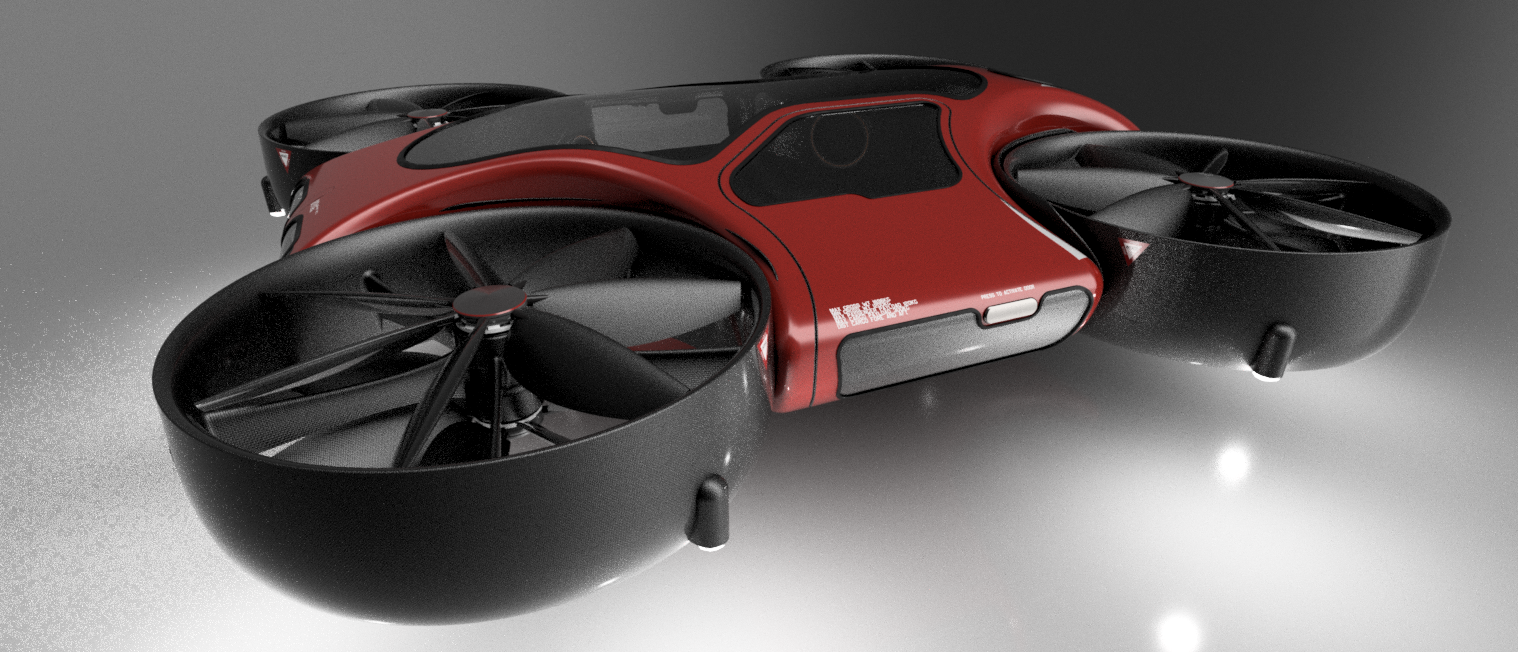
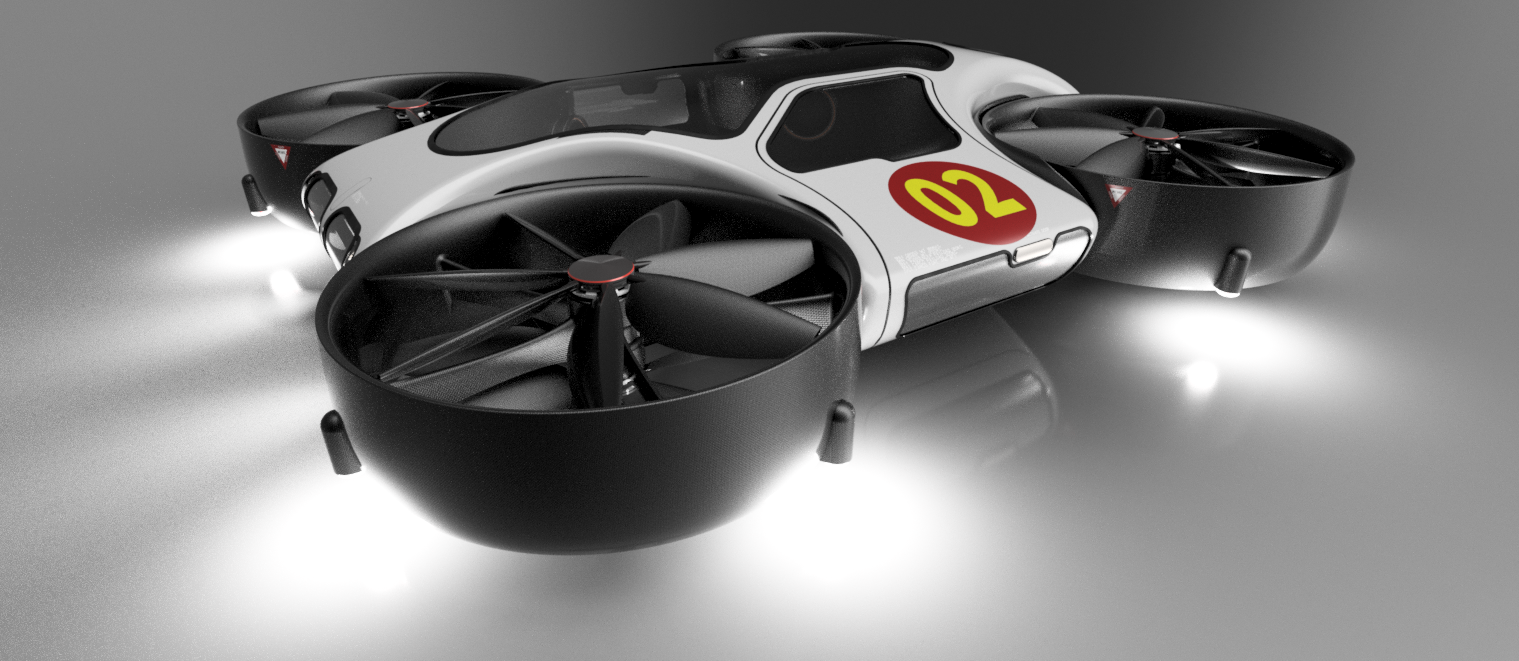
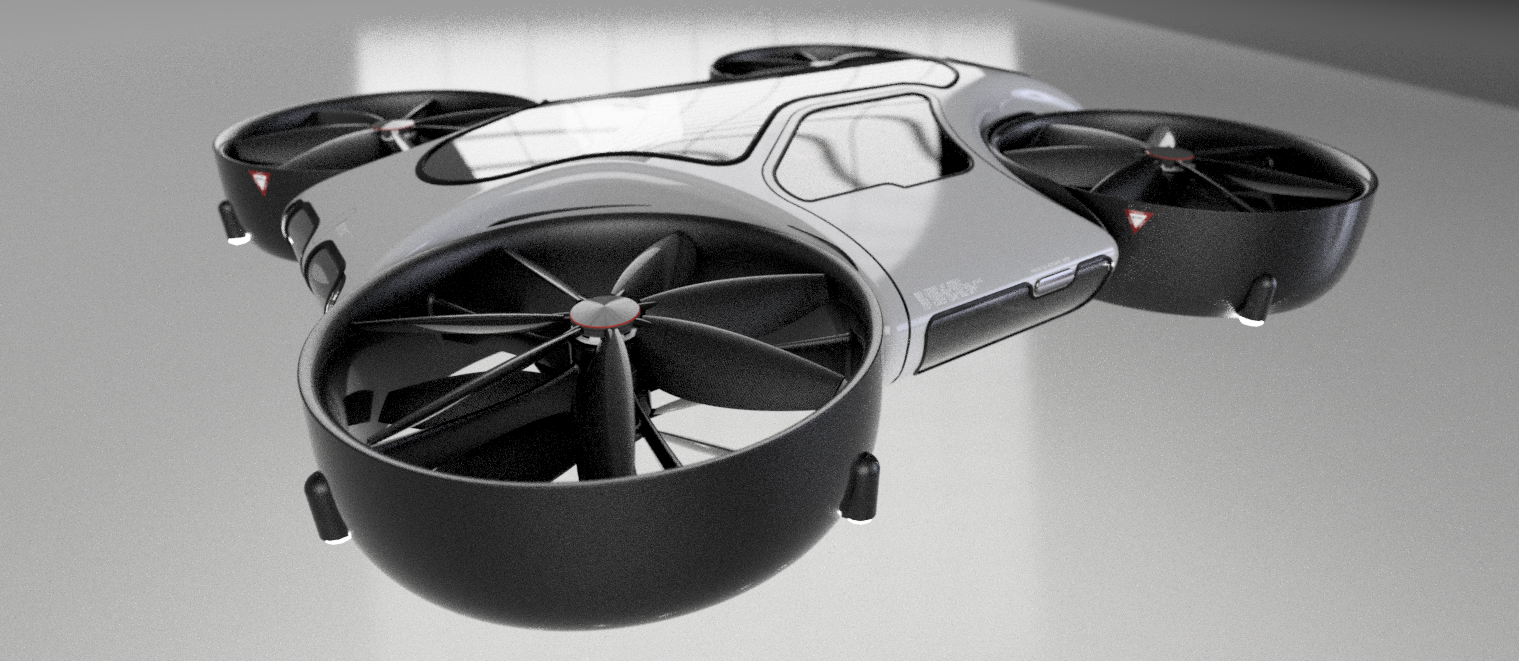
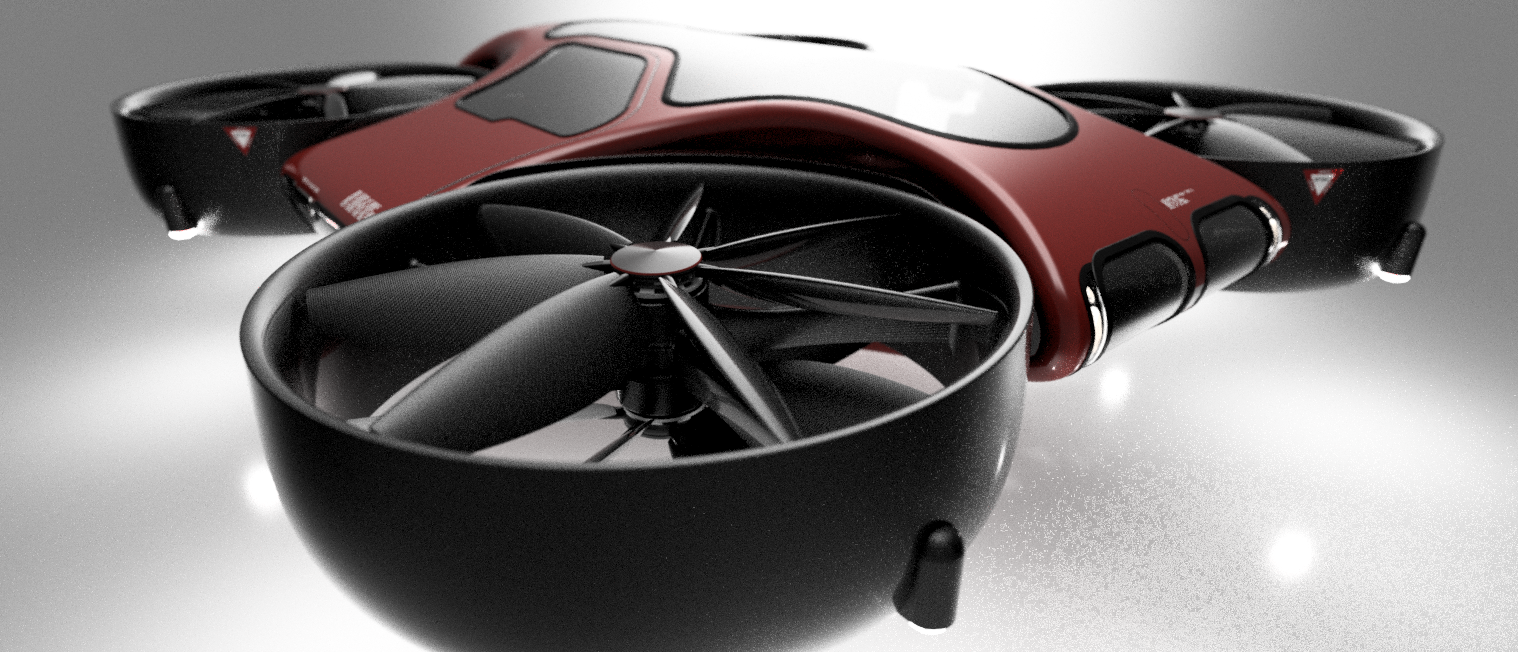
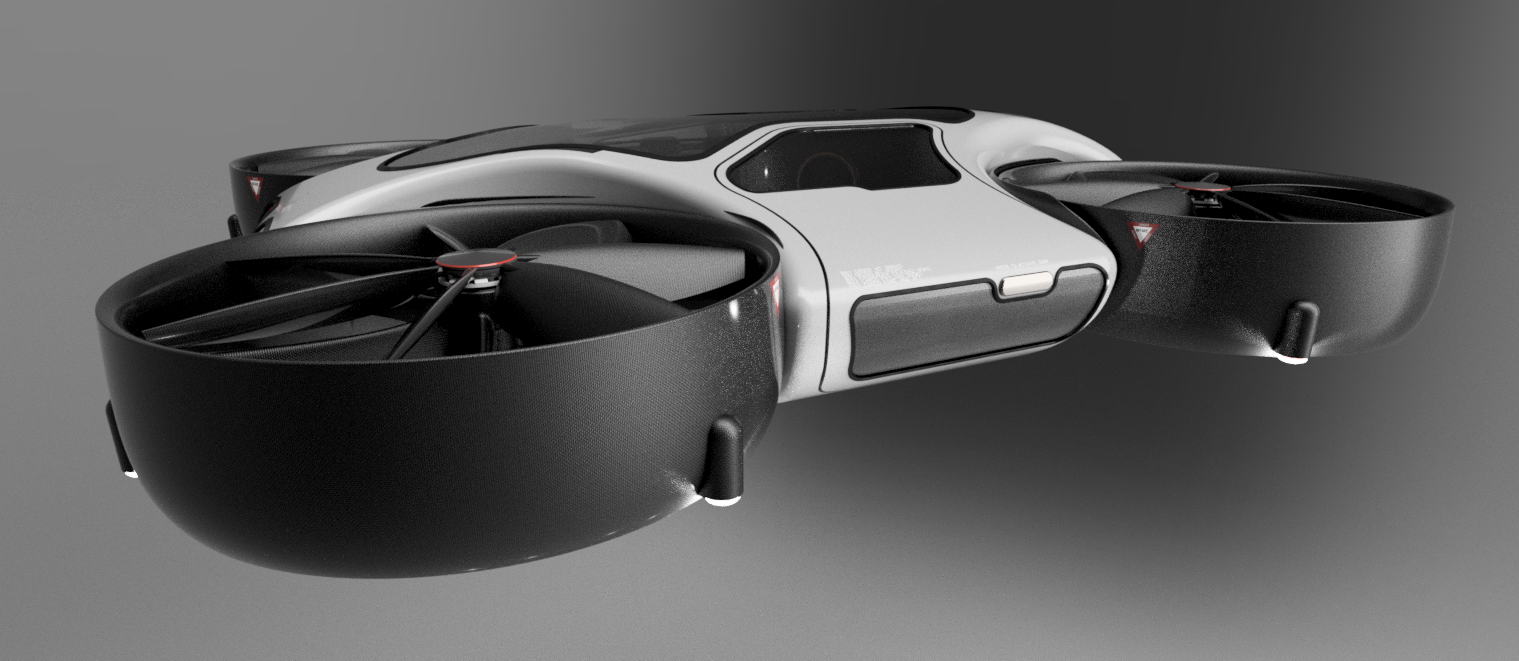
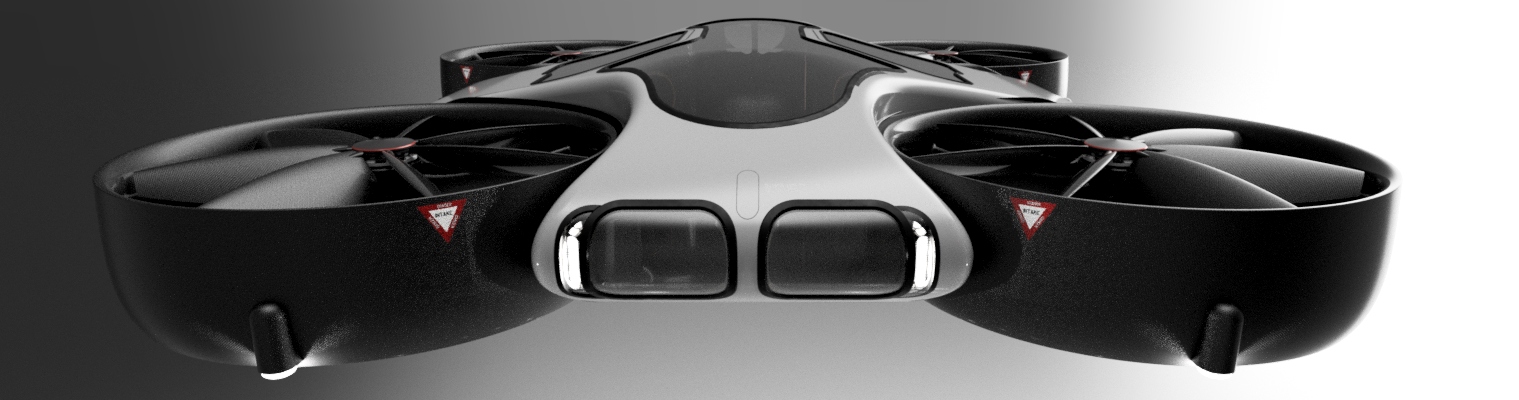
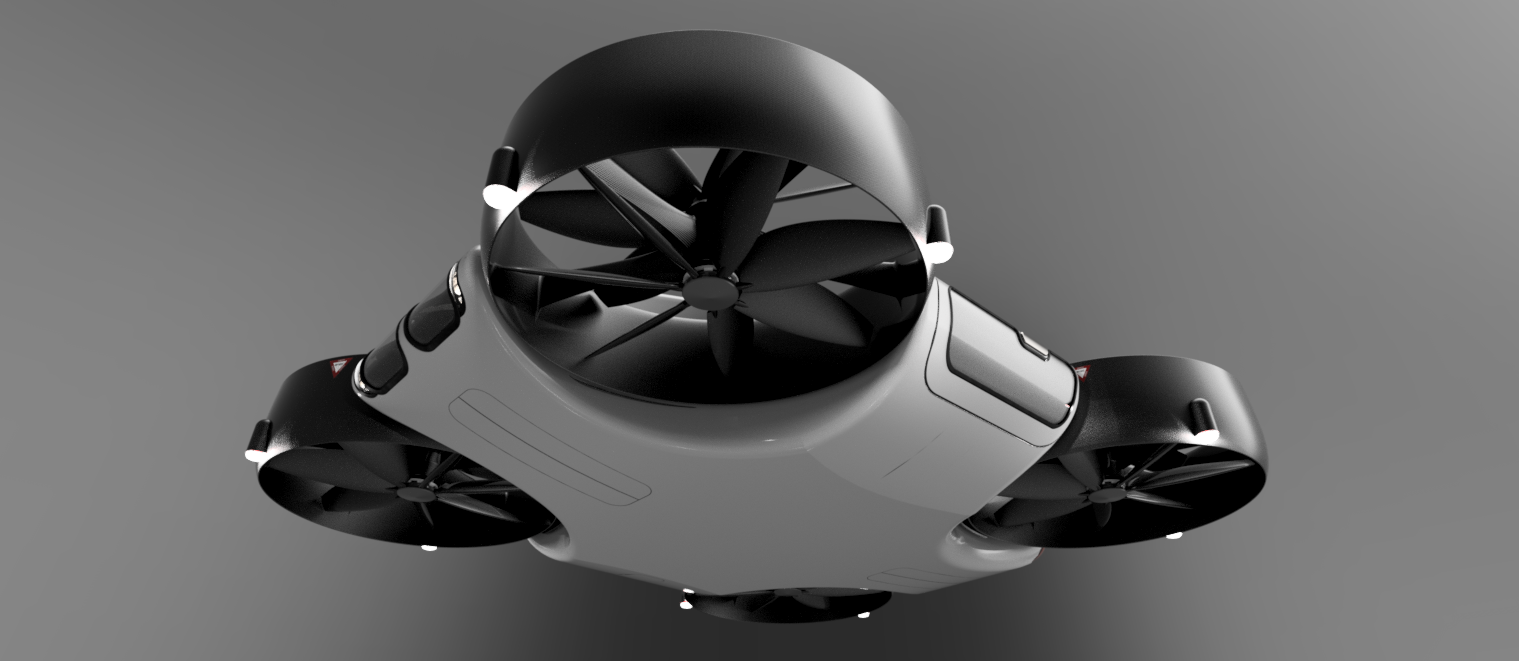
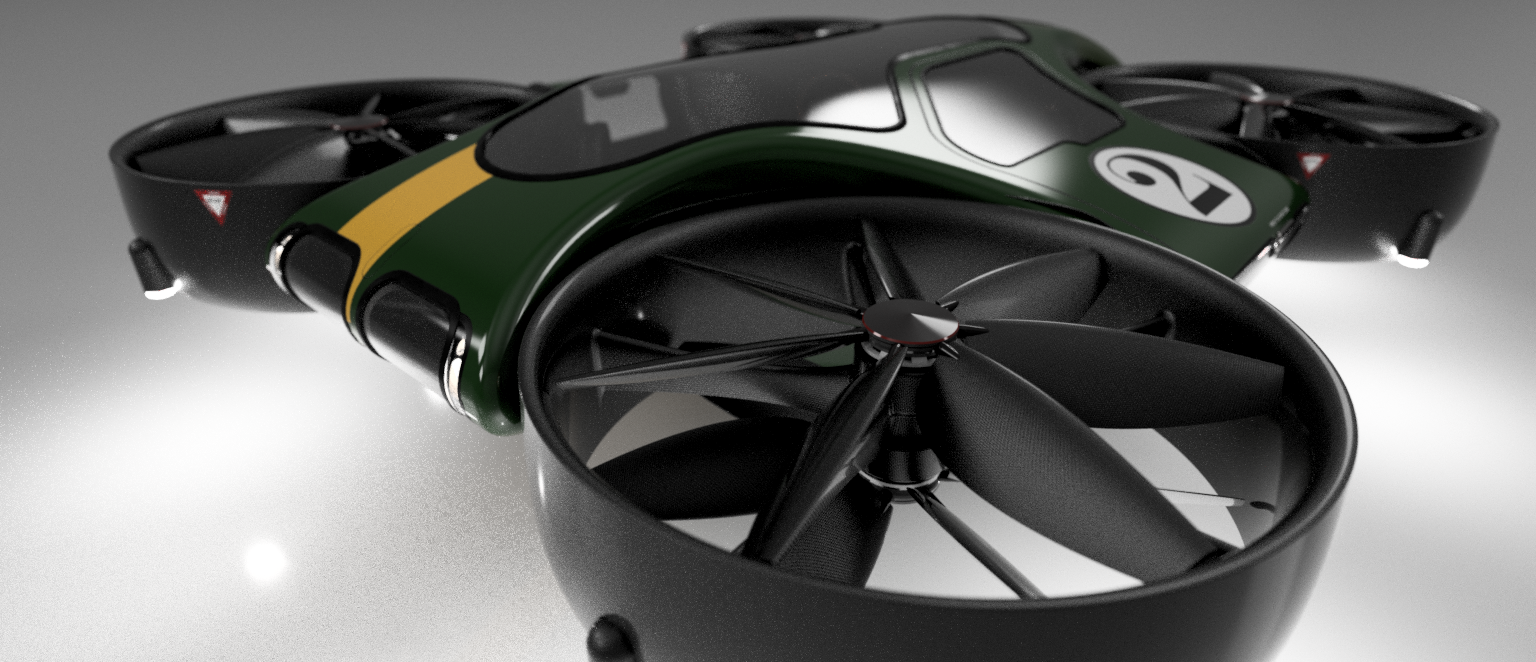
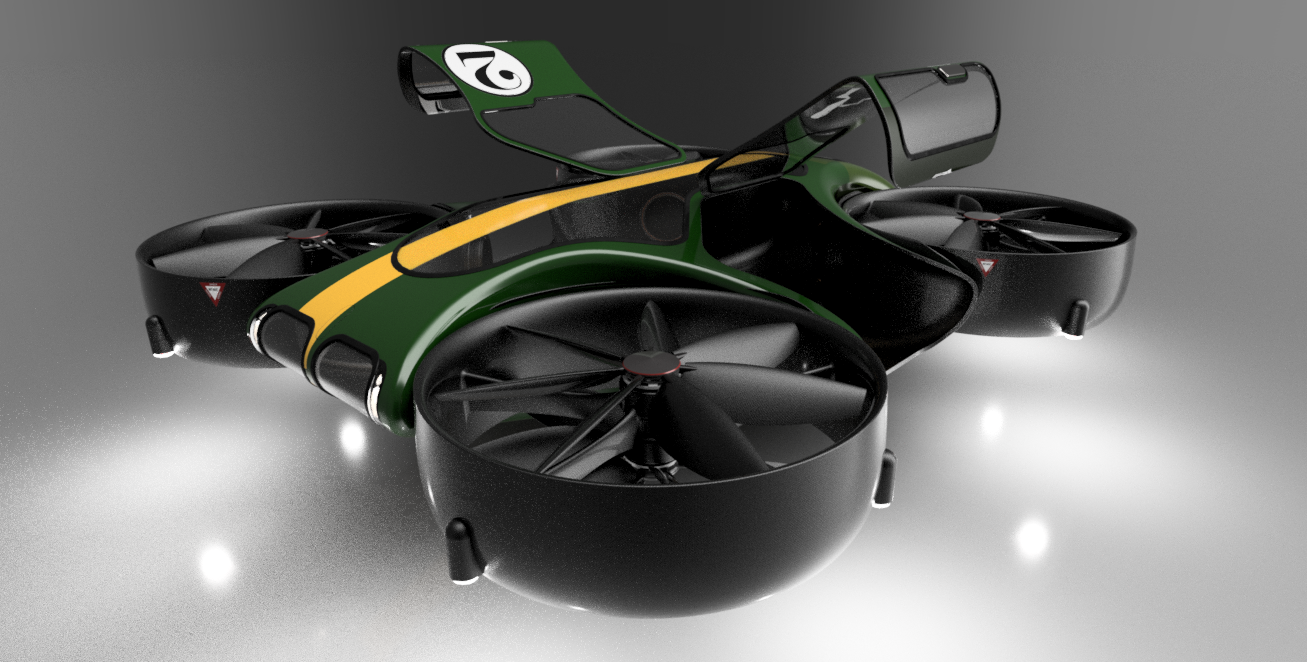